Wool Environment part--II
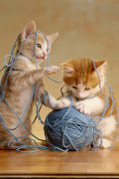
Environmental Wool Science
Developments
Pesticides
Pesticides are used to keep sheep healthy but their
residues can remain in the fleece only to be released
when the shorn wool is scoured - a process in which
dirt and grease are washed from the raw wool. In the
past, the wastewater from wool scouring containing these
residues has added to contamination of rivers. Although
all scouring effluent is treated before discharge into
rivers, traces of "hard" pesticides entering rivers,
such as lindane, exceeded environmental quality standards.
All The Woolmark Company member countries have effective
bans on the use of toxic and persistent organochlorine
and arsenic based pesticides. Only biodegradable chemicals
are permitted and these are applied in a controlled
way which minimises residues. The bans on organochlorines
and arsenic are policed by the wool authorities in each
member country through random testing and 'traceback'
schemes. In Australia, the program has been very successful
and has led to the effective elimination of organochlorine
and arsenic in the wool clip.
Chemical treatments are still required to protect sheep
from infestation by parasites but efforts are made to
reduce the frequency of treatments and to encourage
use of more controlled ways of administering these chemicals.
Only biodegradable chemicals are licensed for use in
The Woolmark Company Member countries. Jetting, showering
or striping are commonly used treatments today in The
Woolmark Company member countries. Older, less precise
methods such as immersion dipping are rarely used.
Apart from pesticide bans, improvements in scouring
technology have been developed alongside alternative
methods of cleaning the effluent on site and some scouring
plants produce very little effluent at all.
Dyeing
Wool, like all other fibres, is usually dyed. Some dyes
include heavy metals which do not break down in the
environment. The problem of unacceptable levels of these
heavy metals in dyeing effluent is common to all textile
fibre dyeing.
Dyes containing chromium are used
extensively in the wool textile industry because of
their high colour fastness and the wide range of colours
available at an economic cost. In some cases there are
no alternative dyes which give equally high performance
especially for the popular fashion shades of black and
navy blue.
The Woolmark Company and major dyestuff manufacturers
developed low chrome effluent dyeing techniques which
are now used commercially. The effluent from these new
techniques meet existing and proposed limits for chromium
residues in dyeing effluent.
In addition, developments improving dyeing techniques
for pre-metallised dyes have reduced the residual levels
of heavy metals in these effluents.
In 1991, The Woolmark Company developed and implemented
a Guide to Good Environmental Practice in wool dying
which is available to Woolmark licensees and their dyers
around the world. Recently, there has been renewed interest
in the use of natural dyes for wool. These Techniques
were used to colour wool for centuries before the invention
of modern, synthetic dyestuffs. The Woolmark Company
has examined these old methods of application using
environmentally acceptable ways to fix the natural colours
to the fibre. The range of shades is more limited and
the dyes are less colour fast but interesting effects
are possible with natural dyes on natural wool fibre.
Shrink Resistance
To prevent wool felting and shrinking
when washed, shrink-resist processes were developed
where the outer scale layer of each wool fibre is chemically
modified and covered by a thin film of polymer. This
enables the fibres to slide smoothly over one another
when wet.
One shrink-resist process produced unacceptably high
levels of organohalogens (AOX) in effluent. The main
source of AOX arose from chlorine used in the pre-treatment
stage. Smaller quantities arose from the chlorine-containing
polymers also used in the process. German regulations
control the levels of AOX permitted in industrial effluent
including those from the wool textile industry. In the
UK, industrial use of chlorine is also regulated and
processors are required to obtain licenses to operate.
The Woolmark Company, in conjunction with wool research
laboratories (CSIRO in Australia) and chemical manufacturers,
is developing pre-treatments and polymers which do not
use chlorine. Already, low or zero AOX polymers are
available and work is continuing on developing commercial
pre-treatment alternatives to chlorine.
Non- chlorine based shrink resist processes are commercially
available for batch treatments. These do not produce
AOX in the treatment bath and are therefore environmentally
acceptable.
Mothproofing
Wool's natural protein composition makes it vulnerable
to some moths and beetles and mothproofing has been
an integral part of quality wool carpet manufacturing
for many years. It is a mandatory requirement for Woolmark
wall to wall carpeting.
While mothproofing carpets are totally safe in use,
investigations have shown that effluent produced from
conventional mothproofing processes may exceed permitted
discharge concentrations and pollute rivers.
The Woolmark Company has developed
two new processes for the industrial application of
mothproofing agents. These recycle the chemicals and
permit vertically no effluent discharge. "Enviroproof"
is commercially available and is capable of mothproofing
wool with a discharge of only one quarter of a gram
of mothproofing agent per tonne of wool treated.
The second process, currently at the industrial prototype
stage, achieves even better performance. Mothproofing
agent discharges are down to one twentieth of a gram
per tonne of wool processed. Both processes meet current
and proposed industrial discharge concentrations for
mothproofing agents.
The Woolmark Company has also worked with a machinery
manufacturer developing a process for foam application
of mothproofing agents during the carpet backing process.
Applying the mothproofing to the carpet rather than
to the yarn avoids contamination of wastewater yet produces
a fully mothproofed carpet.
Wool
Production and the Environment
In Australia, The Woolmark Company
has its own environmental research program covering
the management of sheep and use of land. The program
examines ways to minimise the environmental impact of
woolgrowing.
In addition, Landcare groups of sheep farmers have initiated
tree planting programs to improve land quality.
Caring for the Future
All fibres, both natural and synthetic, must be processed
to fit them to their chosen uses.
Environmental excellence can only be achieved at the
processing stage by selecting the best raw materials,
using best practices during manufacturing and carefully
considering the environmental impacts of products during
use and disposal.
The Woolmark Company will continue to commit resources
to developing new processing technologies for the wool
textile industry which will reduce the potential for
pollution.
|