The five major steps in
processing worsted yarn are: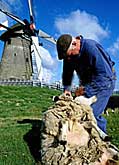
Scouring:
A washing process which removes the dust, suint (sweat)
and wool wax.
Carding:
Rollers covered with teeth tease apart the staples of
wool, laying the fibres nearly parallel, to form a soft
rope called a sliver
Combing:
The comb separates short from long fibres, ensuring
that the long fibres are laid parallel, to produce a
combed sliver called top.
Drawing:
Several tops are drawn out into the thickness of one,
to thoroughly blend the wool and ensure evenness or
regularity of the resulting roving.
Finisher Drawing:
Reduces the roving thickness to suit the spinning operation
and further improve evenness.
Spinning:
Insertion of twist into the yarn in order to give strength
to the finished yarn.

In the woollen process the wool, after carding,
passes through condensers which separates the web into
pre-determined weight strands called slubbing or condensing.
Spinning frames draw these slubbing or condensing out
to the required fineness of yarn and insert twist to
form the yarn.
Worsted fabrics, both woven and knitted, are
often more expensive than woollen spun products due
to the longer raw material to resultant yarn processing
route used. Worsted fabric wears better than a woollen
spun fabric of equivalent weave construction and fabric
weight. For example: Worsted fabrics are preferred for
trouserings, suitings, other garments and upholstery
fabrics where a smooth finish is required. Woollen spun
fabrics are used for jackets, coats, skirts, upholstery
fabrics, rugs and blankets where bulk and textured finishes
are desirable.
|